Die Casting
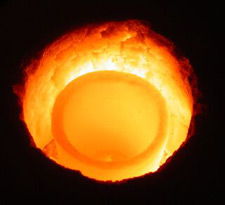
Melting crucible with molten gold
Die casting uses a permanent mold (versus the expendable sacrificial mold) to produce parts from low-strength, nonferrous alloys. The metals are typically low melting point alloys of zinc, such as ZAMAK, a zinc-aluminum blend. The process has been used for years in the making of metal toys and non-stressed hardware items. However, in the late 1960s, poor-quality handguns having major components of zinc-based alloys appeared on the commercial market in large numbers. Many made their way to the forensic firearms laboratories.
The advantages of die casting from zinc alloy are as follows:
- A single mold can produce usable parts over many years.
- The melting of zinc alloys requires less energy than for iron and aluminum alloys.
- The resulting parts are relatively easy to machine.
The disadvantages of die casting from zinc alloy are the following:
- It is difficult to produce precise tolerances.
- Voids or cracks can occur.
- The material strength is poor; wear occurs quickly.
- Untreated zinc alloys corrode easily and the raw surface is unattractive.
Most inexpensive handguns with zinc frames are plated with chrome to cover the physical flaws and rough surfaces. This is not to say that, with care, a reasonably good firearm cannot be made from die-cast components. However, the extra care involved would add significantly to the cost, which is of little interest to low-cost firearms manufacturers.
< Previous Page :: Next Page >